A Comprehensive Guide to Risk Management of Imported Clothing
In the globalized economy, the importation of clothing involves navigating a complex web of risks that can impact the financial health, reputation, and operational continuity of businesses. Effective risk management strategies are essential to mitigate these risks and ensure the smooth operation of supply chains. This article explores the major risks associated with importing clothing and outlines practical approaches to manage them.
Understanding Risks in Imported Clothing
Supply Chain Disruptions
- Natural Disasters: Natural disasters such as earthquakes, floods, and hurricanes can disrupt supply chains and delay shipments. For example, a flood in a region where a significant portion of a particular fabric is produced can lead to shortages and increased costs.
- Political Instability: Changes in government policies, trade wars, and geopolitical tensions can affect the availability and cost of imported goods. Political instability in a sourcing country might lead to unpredictable changes in export regulations, affecting the reliability of supply.
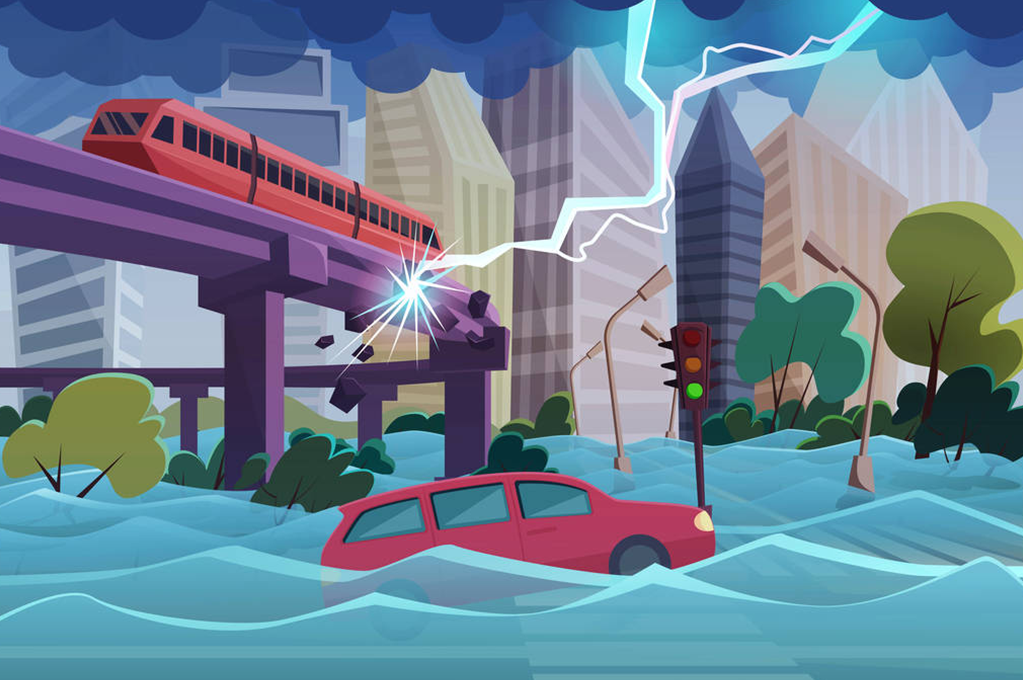
Quality Control
- Manufacturing Defects: Poor quality control at the factory level can lead to defective products that do not meet the required standards. Issues like stitching defects, incorrect sizing, or use of substandard materials can result in returns and reputational damage.
- Counterfeit Goods: The presence of counterfeit goods can tarnish a brand’s reputation and lead to legal issues. Counterfeiting not only undermines brand integrity but also poses a risk to consumers if the counterfeit items are of poor quality or unsafe.
Regulatory Compliance
- Customs Regulations: Non-compliance with customs regulations can result in delays, fines, and even the confiscation of goods. Incorrect labeling, misclassification of goods, or failure to provide necessary documentation can cause significant disruptions.
- Environmental Laws: Regulations regarding the use of sustainable materials and production processes are becoming increasingly stringent. Failure to comply with environmental standards can lead to penalties and damage to the brand’s image.
Financial Risks
- Currency Fluctuations: Variations in exchange rates can affect the profitability of imports. If the local currency depreciates significantly against foreign currencies, the cost of imported goods can rise, impacting margins.
- Payment Delays: Late payments from buyers can strain cash flows and affect the ability to pay suppliers. This can create a domino effect, leading to delayed shipments and potential disruptions in the supply chain.
Strategies for Risk Management
Supply Chain Resilience
- Diversification of Suppliers: Relying on multiple suppliers can reduce dependency on any single source and mitigate the impact of disruptions. For instance, having secondary suppliers for key components can help maintain production schedules if one supplier faces issues.
- Contingency Planning: Developing backup plans for critical supply chain functions can help minimize the effects of unexpected events. This includes having alternative shipping routes, additional warehousing space, and pre-negotiated terms with logistics providers.
Quality Assurance
- Third-Party Audits: Engaging independent auditors to inspect facilities and processes can help ensure compliance with quality standards. Audits can cover everything from material sourcing to finished product quality, ensuring that every step meets the necessary criteria.
- Supplier Certifications: Working with suppliers that hold recognized certifications (e.g., ISO 9001) can provide assurance of quality and ethical practices. Certifications indicate that suppliers have undergone rigorous evaluations and adhere to international standards.
Legal and Ethical Compliance
- Regular Audits: Conducting regular audits of both internal processes and external partners can help maintain compliance with relevant laws and regulations. Audits can be scheduled annually or triggered by specific events, such as changes in legislation or supplier performance issues.
- Transparency Initiatives: Promoting transparency in the supply chain can build consumer trust and demonstrate a commitment to ethical business practices. Initiatives might include publishing supplier lists, conducting social audits, and participating in industry-wide initiatives focused on ethical sourcing.
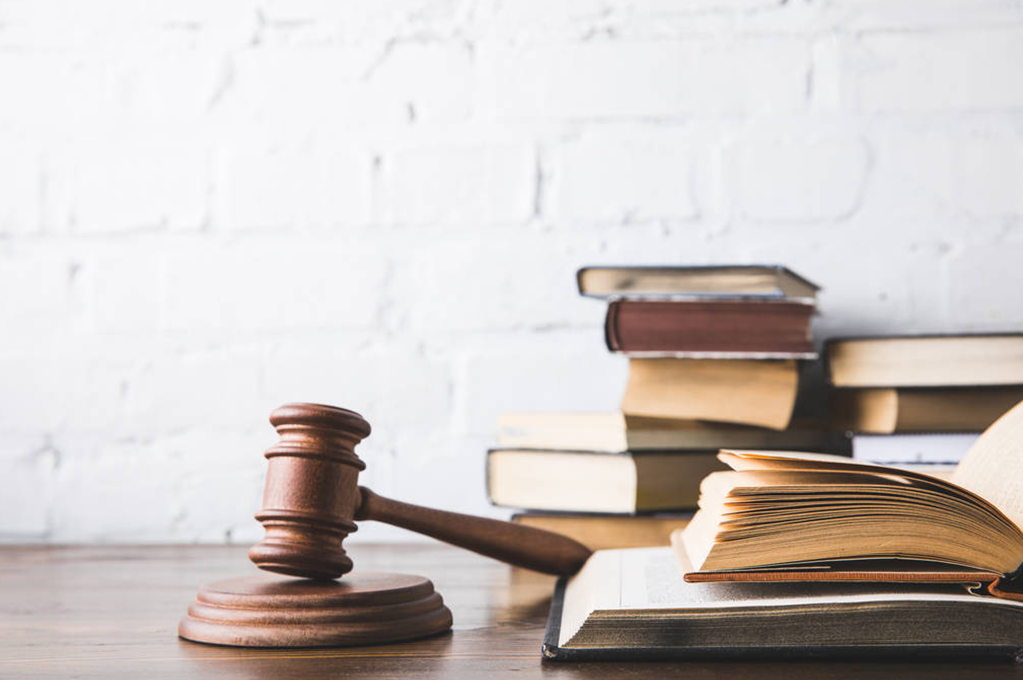
Financial Risk Mitigation
- Hedging Strategies: Using financial instruments such as futures contracts or options can protect against adverse movements in currency exchange rates. Hedging can lock in favorable exchange rates and reduce the volatility of costs.
- Credit Insurance: Obtaining credit insurance can safeguard against losses due to non-payment by buyers. Credit insurance policies can provide financial protection and enable companies to extend credit terms with more confidence.
Technological Solutions for Risk Management
Advanced Analytics
- Data Analysis: Leveraging big data and analytics can help predict potential disruptions and identify trends that might affect the supply chain. Analyzing historical data can reveal patterns that might signal future risks, such as seasonal variations in shipping delays.
- Predictive Modeling: Using machine learning algorithms to forecast demand and identify risks can improve inventory management and reduce waste. Predictive models can help optimize stock levels, reducing the need for excess inventory and freeing up capital.
Supply Chain Visibilit
- Blockchain Technology: Implementing blockchain can increase transparency and traceability, ensuring that all parties have access to verified information about the origin and journey of goods. Blockchain can provide an immutable record of transactions, enhancing trust among stakeholders.
- IoT Devices: Internet of Things (IoT) sensors can provide real-time data on environmental conditions during transport, helping to ensure the integrity of goods. Sensors can monitor factors such as temperature, humidity, and shock, alerting stakeholders to any issues that might compromise the quality of the products.
Stakeholder Engagement
Collaboration with Suppliers
- Partnership Agreements: Establishing long-term partnerships with suppliers can foster mutual benefits and shared responsibilities. Partnership agreements can outline joint goals, such as improving sustainability or reducing lead times.
- Joint Risk Assessment: Conducting joint risk assessments can help identify vulnerabilities and develop collaborative solutions. Joint assessments involve working closely with suppliers to evaluate risks across the entire supply chain and develop mitigation
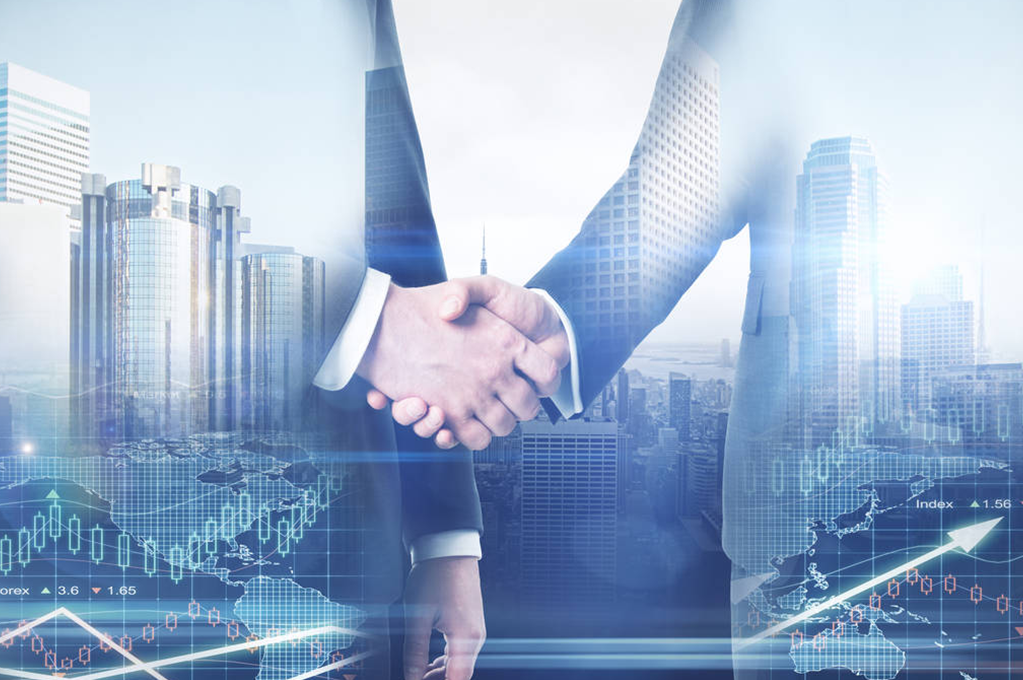
Customer Engagement
- Communication Channels: Maintaining open lines of communication with customers can help manage expectations and address concerns proactively. Regular updates about shipment status and expected delivery dates can enhance customer satisfaction.
- Feedback Loops: Creating mechanisms for collecting customer feedback can provide insights into areas of improvement and potential risks. Feedback loops can include online surveys, customer service hotlines, and social media engagement.
Continuous Improvement
Training and Development
- Employee Education: Providing regular training on risk management principles and techniques can ensure that all team members are aware of their roles in risk mitigation. Training can cover topics such as identifying risk indicators, responding to incidents, and understanding regulatory changes.
- Cross-functional Teams: Forming teams that bring together expertise from different departments can lead to more holistic risk management strategies. Cross-functional teams can include representatives from procurement, logistics, finance, and marketing to ensure a comprehensive approach to risk assessment and mitigation.
Performance Metrics
- Key Performance Indicators (KPIs): Developing KPIs related to risk management can help track progress and identify areas needing improvement. KPIs might include incident response time, supplier audit scores, and compliance rates.
- Benchmarking: Comparing performance against industry standards can highlight gaps and inform strategic planning. Benchmarking can involve participating in industry surveys, attending conferences, and collaborating with industry associations to stay informed about best practices.
Effective risk management is crucial for businesses involved in the importation of clothing. By understanding the specific risks associated with global trade and implementing proactive strategies, companies can enhance their resilience and competitiveness. Leveraging technology, fostering stakeholder engagement, and focusing on continuous improvement can further strengthen risk management frameworks. In an era marked by rapid change and increasing complexity, a robust approach to risk management can provide the stability and agility needed to succeed in the dynamic world of international trade. Whether it’s anticipating natural disasters or addressing ethical concerns, proactive and comprehensive risk management is key to navigating the challenges of importing clothing successfully.
I hope this article can help you further understand Risk Management of Imported Clothing. If you want to learn more about importing clothing and transportation from China, you can visit our homepage or contact us directly!